System upgrades resulting in lower emissions
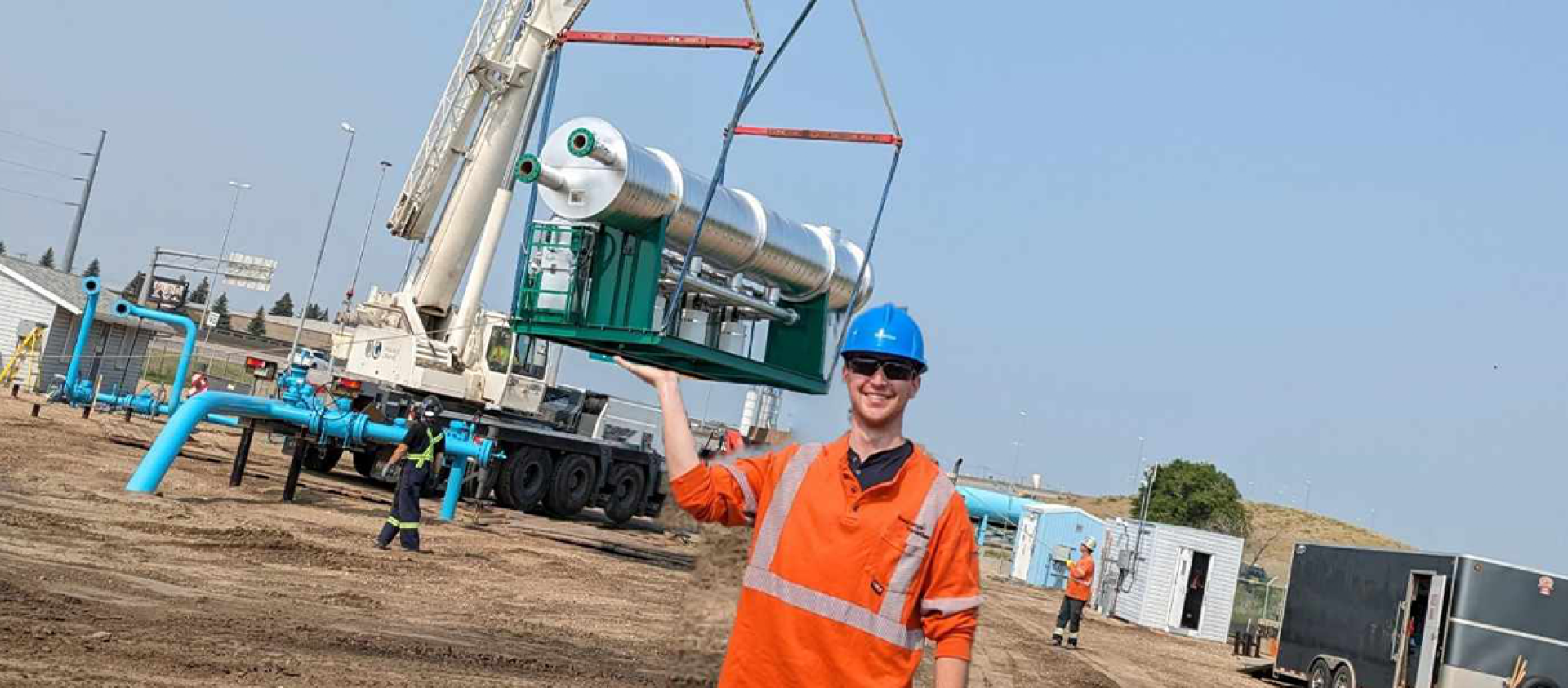
At SaskEnergy, we are committed to reducing emissions from our operations by 35 per cent by 2030.
A lot of the work to achieve this goal involves technological upgrades to our system through three focus areas — vent gas reduction, optimization and renewable electricity.
New systems
We are designing and installing new flare systems at our stations across Saskatchewan, to cut down the amount of gas that is vented through our operations.
Flare systems are regularly shown on TV news, or you may have noticed them while driving by – a flame coming from the top of a tall thin pipe at a SaskEnergy facility.
About 25 per cent of SaskEnergy’s emissions come from venting, whether it’s from gas line maintenance or through devices that vent gas by design.
A flare system combusts gas that would be vented. This transforms the methane in the gas into carbon dioxide (CO2). Flaring reduces emissions by an estimated 80 per cent compared to venting.
We are also reducing emissions through using more renewable energy. We have installed large-scale solar power systems at four SaskEnergy facilities so far — in Regina, Swift Current and Success.
Equipment upgrades
Replacing old equipment with new, more efficient equipment helps us reduce emissions. This includes our line heaters.
SaskEnergy has more than 450 line heaters operating at our facilities across the province. Their purpose is to heat natural gas that’s in a gas line, wherever pressure is reduced, to keep gas flowing.
Like a furnace in your home, line heaters are fueled by natural gas. And, just as furnace technology has improved over the years to be more efficient, so has line heater technology!
In recent years, most of our line heaters have been replaced with new models that use less fuel gas to operate. We are continuing to replace old line heaters each year. By 2030, we’ll have upgraded about 85 per cent of our line heaters.
Proactive monitoring
We also keep a close eye on our infrastructure to ensure everything is running optimally.
Through our proactive Leak Detection and Repair (LDAR) program, we are completing hundreds of equipment surveys each year to identify and repair leaks at our above-ground transmission and storage facilities.
We use infrared cameras and other tools to survey our compressor stations and meter stations numerous times each year, and more than what is required through regulations.
Since the LDAR program began in 2020, more than 1,500 leaks have been identified and repaired. Last year, we achieved a 55 per cent year-over-year reduction in the average number of leaks per site.